LG CNS Deploys Custom Cooling Approach in Korean Data Centers
IT services provider develops innovative cooling system for use in its own cloud computing data centers
By Jong Wan Kim
LG CNS is a major IT services and solutions provider in Korea. Since 1987, LG CNS has acted as the CIO for LG Group’s affiliates. As of the end of 2014, its data centers provided IT services to LG Group’s affiliates in more than 40 countries, including China, Japan, United States, India, Indonesia, Brazil, Colombia, Malaysia, and several nations in Europe. LG CNS also offers services government, public, and financial sector entities.
LG CNS operates four data centers in Korea and one each in Beijing, Nanjing, New Jersey, and Amsterdam, The Netherlands. Three of its domestic data centers are located in or near Seoul, Korea’s capital; the other one is in Busan, which is located in southeast Korea and is the country’s the second largest city (see Figure 1).
LG CNS and its operating technicians and potential customers all view energy efficiency as crucial to controlling costs. In recent years, however, rapid developments have dramatically improved IT performance. At the same time, new processors produce more heat, so data centers must provide more space for power and cooling infrastructure. As a result, LG CNS concluded that it needed to develop a cooling system optimized for very dense data centers. They expected that the optimized cooling system would also be more energy-efficient.
LG CNS developed and applied an optimized custom cooling system concept to its new 40-megawatt (MW), 32,321-square-meter (m2) Busan Global Cloud Data Center, which is the largest in Korea. This facility, which opened in 2013, serves as the company’s hub in northeast Asia (see Figure 2). The Busan Data Center can accommodate 3,600 servers at 6 kilowatts (kW) per rack.
The Busan Data Center makes use of whole-building, chimney-style hot-air exhaust and a hybrid cooling system (LG CNS calls it a Built-up Outside Air Cooling System) that the company developed to improve upon the energy efficiency it achieved in its existing facilities, which used a packaged-type air conditioning system (existing packaged-type air conditioning system). In addition, LG CNS developed its Smart Green Platform (SGP) software that automatically controls the unique cooling system and other data center components to achieve free cooling for eight months of the year without running chillers. The annual average PUE is estimated to be 1.39, with a minimum of 1.15 in the winter. After seeing positive results at the Busan Data Center, LG CNS decided to apply the cooling system to its Inchon Data Center, which was built in 1992 and was the first purpose-built data center in Korea.
THE BUSAN DATA CENTER SITE
The Busan location provides three advantages to LG CNS: geographic, network connectivity, and proximity to new customers.
• Geographic: Data centers should located be where the risk of natural disasters, especially earthquakes, is low. Korea has relatively little seismic activity, making it a good candidate for data centers. The building is also set on an elevation that is higher than the historic high water levels.
• Network Connectivity: Korea has four active submarine connections: the Busan cable, the Keoje cable, the C2C Basan cable, and Taean cable, which connect to the APCN, APCN-2, C2C, China-US CN, EAC, FNAL/RNAL, FLAG FEA, RJCN, R-J-K, and TPE submarine cable systems. This connectivity positions Busan as an IT hub for Asia-Pacific (see Figure 3).
• New customers: Development plans promise to transform Busan into a global IT hub with many foreign companies accessing its infrastructure resources.
COOLING THE BUSAN DATA CENTER
Utilizing cold outside air may be the best way to reduce energy use. From June through September, outside air temperatures near Busan are often greater than 30°C (86°F) and humid, so it cannot be used for cooling (see Figure 4). To meet this environmental challenge, LG CNS developed a system that converts space that normally houses CRAC units into a functional CRAC. Although LG CNS developed the system for its new Busan Data Center, it subsequently applied it to the existing Inchon Data Center. In the existing data center, this transformation involved disassembling the CRACs. In both new and legacy retrofit applications, LG CNS utilized the walls of the CRAC room as CRAC surfaces and its aisles as paths for airflow.
EXISTING PACKAGED-TYPE CRACS
The existed packaged-type air conditioning system used in existing LG CNS facilities includes an air supply louver, outside air chamber, air supply duct, mixing chamber, filter, humidifier/cooling coil, and fan. These systems require less space than other systems (see Figure 5-7). The existing packaged-type air conditioning system used at LG CNS facilities has three operating modes that vary by outside temperature. At ≈8–16°C (46-62°F), existing packaged-type CRACs provide additional cooling to supplement the outside air; and when the temperature is more than 16°C (62°F), the CRAC is fully operational and no outside air is supplied. When the temperature is below 7°C (45°F), the system uses 100% outside air and the CRAC is not in operation. This is accomplished by stopping the compressors where dedicated air-cooled DX CRACs are in use and the chillers where chilled water CRAHs are in use. Both types are used in LG CNS facilities. When outside air is supplied only the internal fan of CRAC is required, and when the temperature increases the CRAC begins to operate. In Korea, this system yields 100% compressor savings only from December to February and partial energy savings only from October to November and March to May. Limits to the system include:
• The small air supply duct limits the airflow and requires more fan energy. In addition, the narrow inner space makes it difficult to access for maintenance.
• Winter air in Korea is quite dry, so humidification is required during the winter when 100% outside air cooling is possible. However, the size of the CRAC limits its ability to humidify, which causes inefficiencies.
• The existing packaged-type air conditioning requires space for maintaining plumbing, including pipes and ducts.
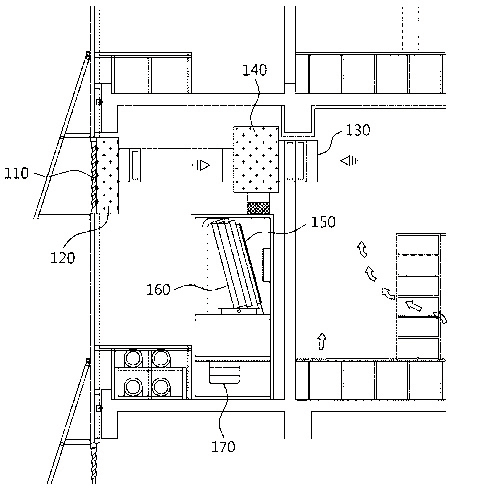
Figure 5. Diagram of existing outside air conditioning (air supply louver 110, outside air chamber 120, air supply duct 130, mixing chamber 140, filter 150, humidifier/cooling coil 160, and fan 170.
BUILT-UP OUTSIDE AIR COOLING SYSTEM
LG CNS created a task force team (TFT) comprising Operations, cooling system vendors, consulting firms, construction personnel, and other relevant professionals to develop a method of improving the flow of outside air for cooling interior white spaces. The TFT investigated new approaches for approximately 10 months, including pilot testing.
The TFT focused on three things:
• Introducing more outdoor air to the computer room
• Controlling the temperature of the static air supply by mixing outside cold air with the inside heated air
• Controlling the airflow of exhaust hot air by maximizing airflow to the outside.
The main concept that resulted from the investigation involves:
• Utilizing the building floor and ceiling as a duct and chamber
• Customizing the size of the CRAC room walls to meet cooling demands
• Increasing humidification efficiency by making the path that air travels longer after it passes through the cold water coil
• Creating a separate pathway for exhausting hot air
• Utilizing a maintenance space as a duct for the CRAC while it is operating and as a maintenance space when it is not.
The Built-up Outside Air Cooling System applied in LG CNS’s new Busan uses outdoor air and built chimneys to exhaust heat generated by the servers, which reduces energy consumption (see Figure 8). In the company’s existing data centers, the width of the packaged-type CRAC was about 2.5 meters (m). The Built-up Outside Air Cooling System should be 4-5-m wide in order to increase the volume of outside air used for cooling. This change, however, increases the construction costs and the size of the building, which can be a significant expense because of the high cost of real estate in Korea. Saving energy is important, but larger equipment and space requirements for infrastructure can reduce IT white space. To address these issues, the width of the additional space required to supply outdoor air in the Busan Data Center is 3 m.
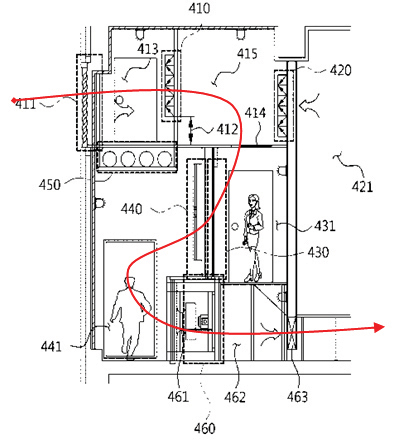
Figure 9. Sectional view of Built-up Outside Air Cooling System
OA Damper (410): Damper to control the outside air supply
OA Louver (411): Opening to introduce the outside air supply and keep rain and sunshine out
RA Damper (420): Damper to control the indoor air
Filter (430): Filter to remove dust from outside and inside
Coil, Humidifier (440): A water mist humidifier to control humidity and a coil for cooling air supplied inside
Main Pipe (450): Pipe to provide supply and return water
Fan (461): Fan for supplying cold air into internal server room
Because of the importance of saving space, LG CNS tested various designs to determine that an S-shaped design would provide the optimum airflow in a small space (see Figure 9). In addition, the system supplies additional outside air using the Built-up Outside Air Cooling System’s internal fan. Care also has to be taken to separate the supply and exhaust air paths to ensure that the mixed air does not come into upper computer room. This task can be complicated in Korea, where most Korean data centers are at least five-stories high. To solve this issue, LG CNS put the cold air supplies on either side of the Busan Data Center and the exhaust in the middle passage to its roof. The company calls it “Chimney,” the wind way (蠾‘).
MOCK-UP TEST
As soon as the design was complete, LG CNS made a separate testing space to determine how changes in ambient temperature would change temperatures in the computer room and evaluate the SGP software (see Figure 10 and 11). LG CNS also used the space to evaluate overall airflow, which was also satisfactory, because the system utilized the entire CRAC room. Coil static pressure, increased airflow, mixing efficiency, utilization of maintenance space, and humidification efficiency also checked out well, (see Figure 12-14) and it was determined that the overall system would work to extend the period in which outside air could be used. LG CNS expected 19% power savings compared to the existing packaged type CRAC.
OPERATION OF BUILT-UP COOLING
The Built-up Outside Air Cooling System has three modes of operation: full outside air mode, mixed mode, and circulation mode. Full outside air mode introduces 100% outside air by means of a damper installed on the building exterior. This mode is used when temperatures are ≈16–20°C (62-68°F) from March to May and September to November. Air enters the building and passes through a mixing chamber without mixing with hot air inside the computer room. If the temperature of the supply air in the computer room is lower than appropriate, the system automatically changes to mixed mode. Full outside air mode was designed to meet LG CNS’s service level agreements (SLA) at outside air temperatures up to 20°C (62-68°F), and LG CNS found that it could maintain Cold Aisle temperatures of 20–21°C (68-70°F) when the supply air was below 20°C (68°F). In fact, LG CNS found that it could still meet its SLAs even when outside air temperatures reached 23°C (73°F). At that outside air temperature the maximum temperature in front of the servers is ≈23–24°C (73-75°F), which still meets LG CNS’s SLAs [23~25°C (73-77 °F) air at the servers]. LG CNS believes that the fast airflow generated by using a whole room as a big CRAC contributes to maximizing cooling from the outside air.
When the ambient temperature is less than 16°C (62°F), the system operates in mixed mode. In this mode of operation, the system of operation mixes outdoor cold air and warm air before introducing it into the computer room. Sensors just inside the building’s outer wall measure the air temperature and adjust the outside damper and the computer room vent dampers to supply air to the computing room at the proper temperature. Circulation mode activates when the outside temperature is greater than 23°C (73°F). At those high temperatures, the outside damper is closed so that no outside air is introduced. Instead air cooled by cold water from the chiller system is introduced into the computer room. By opening the computer room vent dampers 100% while the outside damper remains closed, 4–8°C (39-46°F) cold water from the chiller cools air to the appropriate temperature to supply the computer room.
In Busan, the chiller operates at 100% over 25°C (77°F). Therefore LG CNS sets the optimum temperature data by increasing the temperature of the cooling water from the cooling tower and the temperature of chilled water from the chiller to reduce energy use.
RESULTS
At first there were many doubts about whether Korea’s first Built-up Outside Air Cooling System would reduce energy use, but now many companies view the Busan Data Center as a benchmark. The Built-up Outside Air Cooling System enables LG CNS to use 100% outside air about 8.5 months per year and achieve a PUE of 1.38, which is lower than the design basis PUE of 1.40. The Busan Data Center received the highest rating of A +++ from the Korean Information Technology Service Industry Association (the Association) as a result of a green data center audit. This was the first time a local data center received the Green Data Center Certification since the Association first instituted it in 2012. The Association explained that the amount of electricity saved when the PUE index at a large data center was reduced from 1.80 to 1.40 is equal to the energy that 5,840 ordinary Korean households use for a year (see Figure 15).
APPLICATION OF BUILT-UP AIR COOLING SYSTEM TO AN EXISTING DATA CENTER
LG CNS decided to apply the Built-up Outside Air Cooling System at its Inchon Data Center. It was the first purpose-built data center in Korea in 1992 and has been operating more than 20 years. Energy efficiency is relatively low because the servers are not arranged in a Hot Aisle/Cold Aisle configuration, even though aging power and cooling equipment have been replaced in recent years. Unlike the Busan site, Inchon provided no separate space to build in, since the servers and the CRACs are both in the computing room. As a result LG CNS had to customize the Built-up Outside Air Cooling System. According to power consumption analysis, the existing packaged type system used in the Inchon Data Center accounted for 36% of the facility’s total energy use, the second largest amount after IT. Air-cooled DX CRACs and chilled water CRAHs used in the facility consumed a high percentage of this energy. LG CNS decided to install the Built-up Outside Air Cooling System as an addition to the existing CRAC system. It was not easy to access the outer periphery where the CRAC is installed from the exterior, so LG cut into the exterior wall of the building. There are two types of CRAC units, down-blower and upper-blower type (see Figures 16 and 17).
The type used on a project depends on the cooling exhaust system. The down-blower type is designed to mix internal air and outside air. It needs to have exhaust temperature sensors, an absorbing temperature sensor, a CRAC exhaust sensor, and an internal air-absorbing sensor. A damper regulates the exhaust and a filter cleans the air supply. The basic concept of the upper-blower type CRAC is very similar but with a different equipment layout. The outside air and mixing chambers ducts of upper blower CRACs are large enough to allow 100% supply air to be introduced into the computing room.
The Inchon Data Center building is a two-layered structure, with down-blower type CRACs on the first floor and upper-blower types on the second floor. LG CNS designed two ways of supplying cold outside air into the computer room and installed a big duct for the down blower and upper blower CRACs to supply outside air from the cut outer wall.
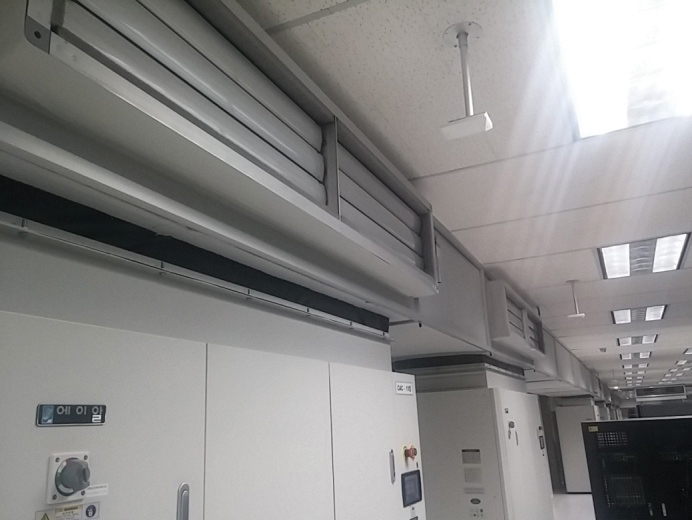
Figure 17. The down (above) and upper blower (below) type of CRACs deployed at the Inchon Data Center
The Built-up Outside Air Cooling System CRAC is installed in a 132-m2 space on the first floor of the Inchon facility. As in the Busan Data Center, the system has three modes, with similar operating parameters (see Figure 18).
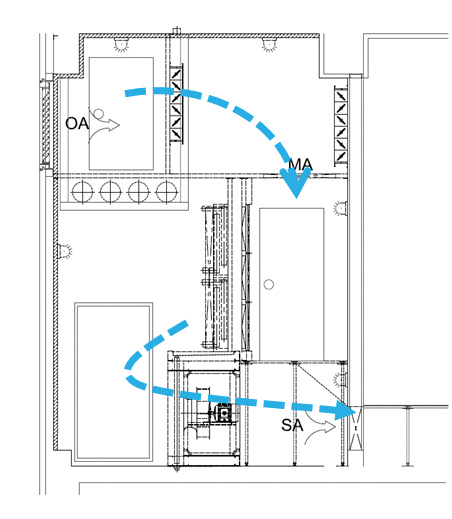
Figure 18. Three modes of operation, outside air mode, mixing mode, and circulation mode (top to bottom)
Even though LG CNS had experience with its system in Busan, the Inchon installation had additional risks because all the computer rooms were in operation. Before the construction phase, a preliminary review of expected risks was conducted so as not to affect the existing servers. In order to protect against dust caused by cutting the outside walls from entering the rooms, LG CNS installed medium density fiberboard (MDF). A temporary finish coating both sides of the exterior wall prevented rain from entering the building. When LG CNS connected the new Built-up Outside Air Cooling System to the existing CRAC, it had to turn off power to the existing CRACs. That eliminated all cooling into the server rooms so portable fans were used to provide cooling air. To maintain the proper temperatures during construction, LG CNS operated the backup CRAC and the temperature of the existing CRAC was set lower than baseline. During the pre-test, the system was able to maintain the computer room temperature for the enclosed space without being affected by the ambient airflow in all three operating modes. However, the computer room is an open type, so the amount of cooling supplied and heating from servers differs from area to area. The solution was to optimize cooling by setting individual targets area by area (see Figure 19).
As the Built-up Outside Air Cooling System CRAC was attached to the inner wall of the computer room, cooling air could not reach the center of the room, so there was a hot spot. Therefore, supply and exhaust vents were installed separately in the center of the room to smooth circulation.
RESULTS AND BENEFITS
As a result of the Inchon retrofit, LG CNS is able to maximize its use of outside air and save 1.9 million kWh in electricity costs. The installation saves LG CNS about US$228,000 in electricity annually, with PUE improving from 1.91 to 1.62 (see Figure 21). There are various methods of improving the efficiency of air conditioning systems and reducing the heat generated in high-density data centers. However, it is much easier to introduce the Built-up Method into a newly built data center than an existing data center, such as the Inchon Data Center. However, LG CNS, through advance planning and risk prevention activities, managed the feat.
ONGOING COMMITMENT
When LG CNS first started planning the Busan Data Center, it built on four main pillars: efficiency, reliability, scalability, and security. And all four goals were integral to achieving overall sustainability. These pillars are the foundations of the data center and ensure that they are able to meet customer needs now and in the future. With that commitment, LG CNS has worked to accumulate technologies in energy efficiency and continue to make efforts to reduce energy use.
Jong Wan Kim is vice president of the LG CNS Infrastructure Unit. He has more than 25 years experience in data center management, distributed systems, and system integration projects. He has implemented operational innovations in the company’s data centers and focused on maximizing productivity based on automation in its next generation data center. Since 2010, Mr. Kim has been president of Data Center Associates, which comprises 28 domestic data center executives. He has consulted the government regarding data center-related policies and encouraged the exchange of technical information among national data centers operators to raise local standards to the global level. More recently, Mr. Kim has concentrated on providing platform-based infrastructure services, including software-defined data centers and cloud computing in distributed computing environments.